Problem
Our customer owned a large commercial office building, and they were struggling with high repair costs and significant downtime due to their aged HVAC equipment. They were budget-constrained so they needed a budget friendly solution, and they needed to remain in operation during the project.
Solution
Mallory & Evans designed a project to fit their current budget which included installation of a replacement Modular Commercial Self-Contained AC unit. This allowed us to bring the 80-ton AC unit into the facility in modules, which eliminated the need for a crane, exterior glass removal, wall demolition and build back of the structure.
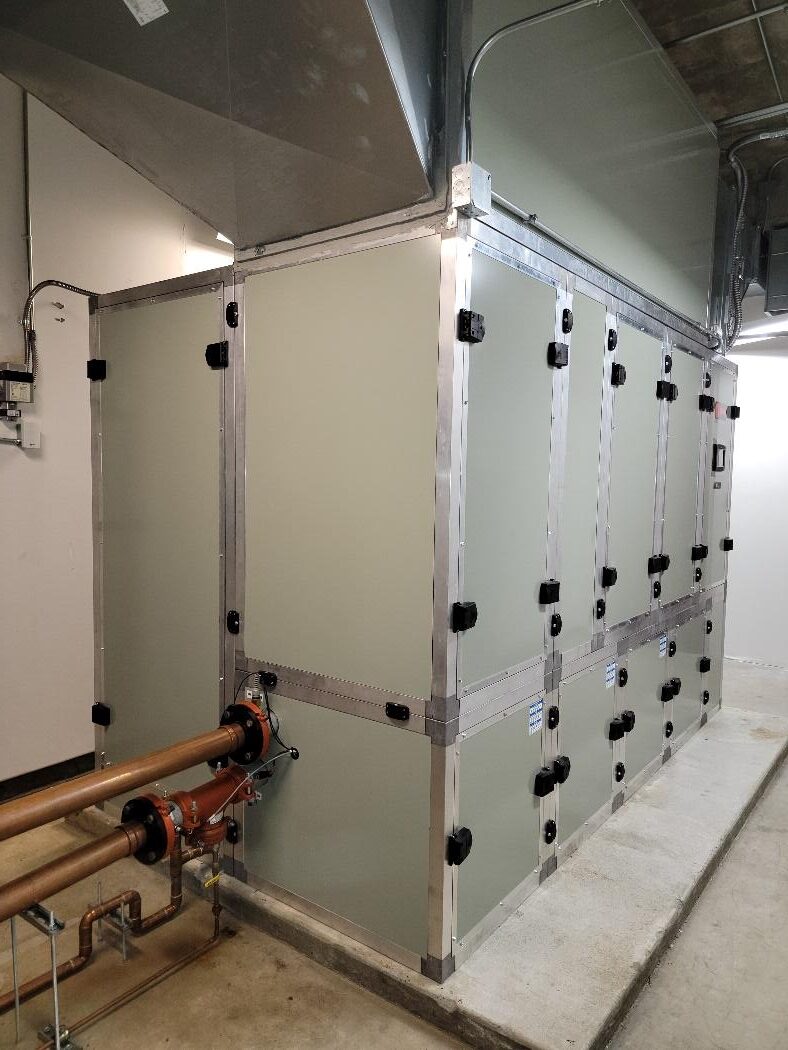
The Situation
This customer had already postponed the decision to replace their equipment because this project posed financial challenges – the equipment was so large that their previous project quotes had included a crane and required the removal of a wall. This would have been expensive for the customer, and almost certain to interrupt their business operations. This customer chose Mallory and Evans because we created a project plan which eliminated this extra risk and expense.
The Work
We were able to bring the individual modules up to the mechanical room using the freight elevator, eliminating the need for wall removal and a larger area shutdown. By utilizing the modular system and effectively completing our project plan, we were able to save the customer significant costs and business interruption.
The Results
All work was performed while continuing to meet the ongoing cooling and heating requirements of the building, and our use of a modular system enabled our customer to keep the entire building open during our work. The project was delivered on time and on budget to the great satisfaction of our customer.
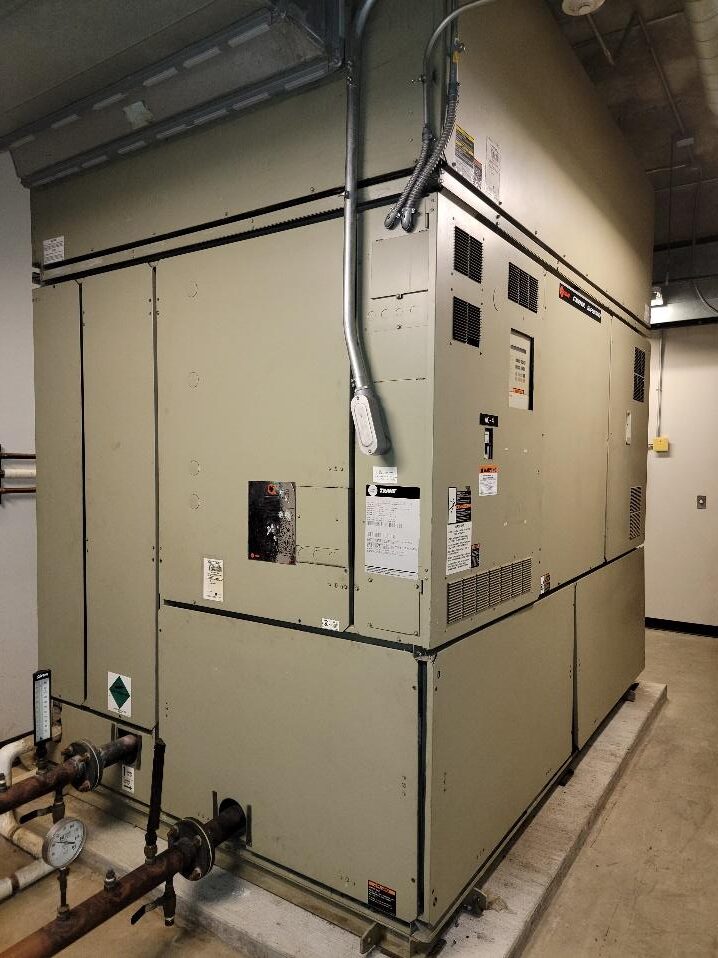
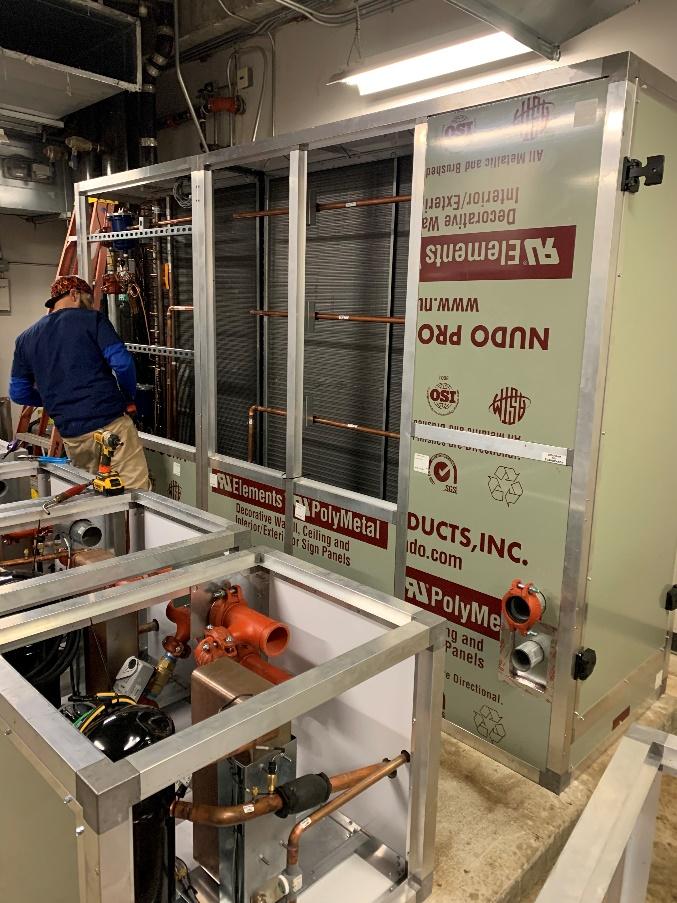
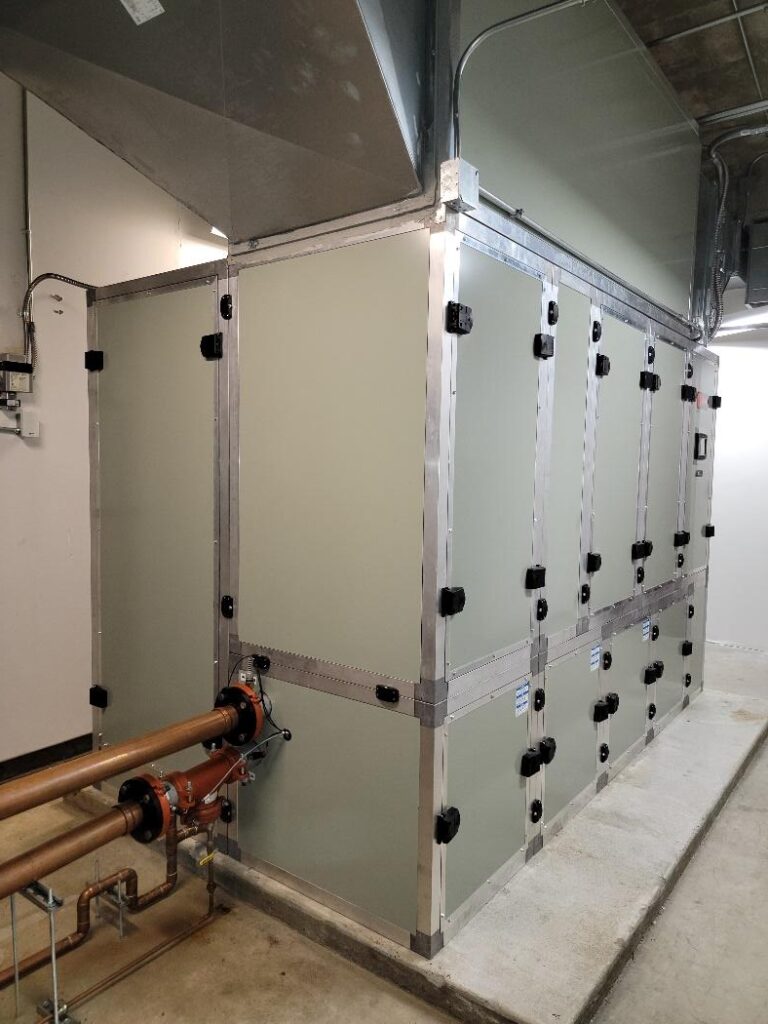